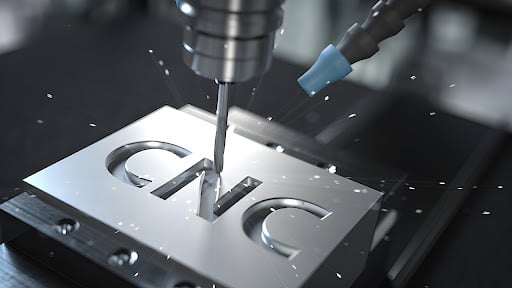
From Design to Finished Product: The CNC Machining Process Explained
Precision and efficiency are of the utmost importance in today’s manufacturing sector. CNC machining is a technology that has greatly improved the manufacturing process for complex parts. CNC machining, also known as computer numerical control, is a subtractive process that converts 3D models into physical objects with high precision. Steps in this process help make complex components for applications as diverse as aerospace and healthcare. This article delves into the CNC machining process and describes its essential steps along with its many advantages.
Design and Digitalization
A CNC machined part’s journey starts in the digital design phase. Skilled engineers use CAD software to model the components in great detail in three dimensions. This digital model is used in production as the blueprint. Engineers pay meticulous attention to design details, making sure that the prototype matches the intended requirements and performance.
Toolpath Generation and Programming
When the CAD model is complete, the toolpaths that control the CNC machine can be created. CAM software, or Computer-Aided Manufacturing software, is used in this context. Cutting tools and material removal from a workpiece are guided by a set of precise instructions generated by computer-aided manufacturing (CAM) software from a digital design. G-Code, a standardized programming language used in CNC machining, is used to convey these instructions to the CNC machine.
Choosing the Right Material
One of the most important steps in CNC machining is choosing the right material for the job. When making this choice, engineers must take into account a number of factors, including the intended use of the part, the mechanical properties needed, and the part’s exposure to environmental conditions. Strong, long-lasting, and resistant to corrosion, metals like aluminum, brass, stainless steel, and titanium are frequently used. However, plastics like ABS, PMMA, and PEEK are favored due to their lightweight and adaptability. The material knowledge ensures that the final product not only functions as intended but also has the desired physical properties.
Preparation of the Workpiece
The manufacturing process moves from the digital realm, where the design and toolpaths have been created, to the physical world. The strength, durability, and function of the finished product all play a role in the material that engineers ultimately settle on. A raw block is then made ready for machining after the material has been selected. The piece of material being cut, known as the workpiece, is fixed to the CNC machine’s table or fixture.
Manufacturing Processes
As the CNC machine begins to carry out the predetermined toolpaths, it is brought to life. Precision cutting is possible because modern CNC machines can move the cutting tools in multiple directions at once. Drills, end mills, and other cutting tools are used to gradually remove material from the workpiece in accordance with the instructions given by the computer. Each necessary feature, such as a hole, pocket, or complex geometry, must undergo this procedure again.
Quality Control and Inspection
CNC machining relies on precision, so keeping tolerances small is essential. Engineers keep a close eye on the machining process to guarantee consistent dimensions and geometries. Furthermore, post-machining measurements and in-process inspections are performed as quality control measures to ensure the final product is up to par with the design intent. All CNC machined components must pass this stringent inspection before being released.
Post-Production and Surface Finishing
Even though CNC machining results in highly precise pieces, the surface finish may still need some work. Sanding, polishing, anodizing, or painting can be used to achieve the desired surface texture, appearance, and corrosion resistance, depending on the application. These additional processes polish the machined parts to perfection, both aesthetically and practically.
Conclusion
CNC machining is an iterative process that bridges the gap between virtual and actual worlds. Intricate programming, careful removal of material, and rigorous quality control are required to realize a concept as a fully functional, high-quality component. CNC machining has become an essential technology in contemporary manufacturing due to its ability to produce complex parts with unrivaled accuracy and efficiency.